A fundamental question that is often asked in the metalworking industry is, “How thin can you cast stainless steel?” It’s a complicated question to answer because numerous variables need to be considered, such as the alloy being used, the size and shape of the casting, and the type of furnace being used. In this blog post, we’ll look at some of the factors that affect how thin you can cast stainless steel and provide some general guidelines.
Various factors go into how thin a stainless steel casting can be. The size and shape of the casting, the alloy being used, and the foundry’s capabilities all play a role in how thin a casting can be made. In general, though, thinner castings tend to be more difficult to produce and have a higher defect rate.
Thin castings can be used in various applications, such as medical devices, automotive parts, and consumer electronics. They offer several advantages over thicker castings, such as reduced weight and increased flexibility. To know more information on stainless steel casting, check out DawangCasting.
Factors Affecting The Thickness Of A Cast Stainless Steel Product
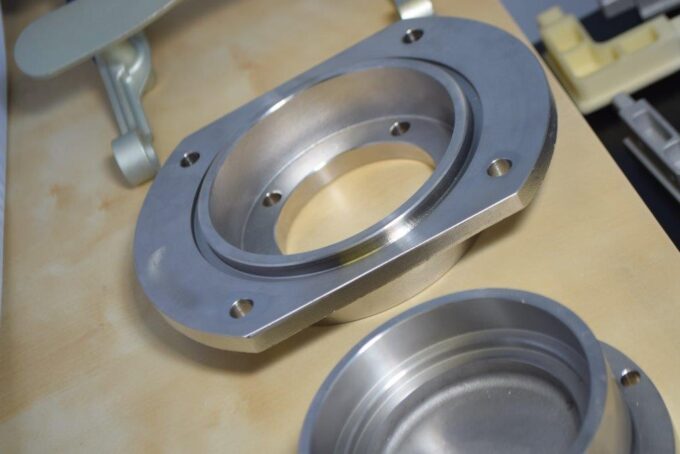
Source:odmetals.com
The Chemical Composition Of The Alloy
Cast stainless steel products are manufactured using an alloy of stainless steel and a small amount of carbon. The chemical composition of the alloy affects the thickness of the cast stainless steel product. Carbon atoms will diffuse into the stainless steel and make it harder. This will cause the product to be thicker than if a lower concentration of carbon was used.
The Casting Process
The casting process is the manufacturing process of producing objects from molten or semi-solid material. The casting process includes pouring the metal into a mold, followed by the removal of the object from the mold. To produce a cast stainless steel product, the metal must be poured into a mold made out of refractory material.
The casting process affects the thickness of a cast stainless steel product. The casting process can cause the thickness of a cast stainless steel product to vary, depending on the type of mold used. A mold with a large surface area can provide you with thin casting compared to a small area.
The Cooling Rate
The cooling rate affects the thickness of a cast stainless steel product because the atoms in the metal are in a high-energy state when it is liquid. When the metal solidifies, the atoms move into their lower-energy states, and this process happens more quickly if the metal cools quickly. If the metal cools slowly, there is more time for the atoms to move into their lower-energy states so that the product will be thicker. If the steel is cooled too quickly, it will be too thin. If it is cooled too slowly, it will be too thick. The best cooling rate for a cast stainless steel product is a moderate rate that cools the steel evenly.
The Pouring Temperature
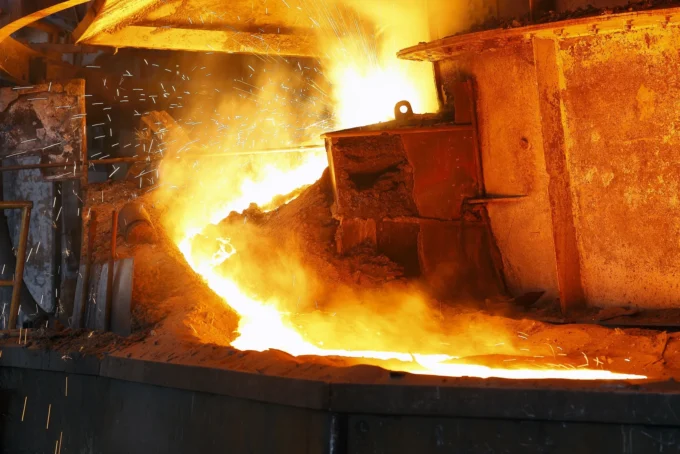
Source:marlinwire.com
The pouring temperature affects the thickness of a cast stainless steel product. If the pouring temperature is too high, the casting will be too thick and have low elasticity. If the pouring temperature is too low, the casting will be thin and have low toughness. The best pouring temperature for cast stainless steel products is between 1600 and 1700 degrees Fahrenheit.
The Mold Configuration
The shape of the mold cavity affects the thickness of the cast product. A deep cavity will produce a thicker product than a shallow cavity. The shape of the mold also affects the casting rate. A mold with a sharp taper will produce a thicker product than a mold with a gradual taper.
Advantages And Disadvantages Of Thin Casting
Advantages:
Stainless steel casting has become a popular choice in various industries because of the many advantages it offers. Some of the benefits of stainless steel thin casting include:
- Durability: Stainless steel is incredibly durable and can withstand much wear and tear. This makes it an ideal choice for applications that require a lot of strength and resilience.
- Flexibility: Stainless steel can be easily molded into various shapes and sizes, making it a versatile option for a wide range of applications.
- Corrosion resistance: Stainless steel casting is a metal alloy of several metals, including chromium and nickel. In its purest form, stainless steel casting is resistant to corrosion. However, when alloyed with other metals, it can be more or less resistant to corrosion. Chromium, in particular, is a very important component in stainless steel casting, as it provides the alloy with corrosion resistance properties.
Disadvantages:
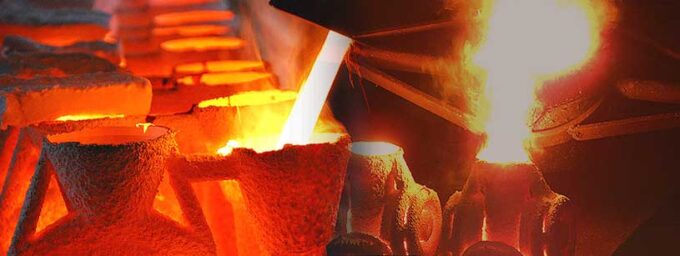
Source:vast-cast.com
There are several disadvantages to using stainless steel casting. There are a few disadvantages to stainless steel thin casting. The first disadvantage is that the process is very expensive. The second disadvantage is that it can be difficult to get a good finish on the castings. The third disadvantage is that the process is very slow, so it is not suitable for high-volume production.
- The high cost of stainless steel casting: The high cost of stainless steel casting is the first disadvantage of this process. This is because the process requires a high level of precision and specialized equipment.
- Limited design flexibility: Stainless steel castings are limited in design flexibility. This is because they can only be made in many shapes and sizes.
- Low production rates: The low production rates associated with stainless steel casting are another disadvantage of this process. This is because the process is very slow and labor-intensive.
- Brittle and can fracture easily: Stainless steel castings are often brittle and can fracture easily because the carbon content is not evenly distributed. The carbon content is higher in the outer layer of the casting than in the inner layer. The high carbon content in the outer layer makes the casting brittle and susceptible to fracture.
Bottomline
This article explored the feasibility of casting very thin stainless steel sheets. By understanding the factors that influence the thickness of the cast, you can take proactive steps to get your best possible outcomes.